Infrared crystal dryer for R-PET Pelletizing/ Extrusion Line
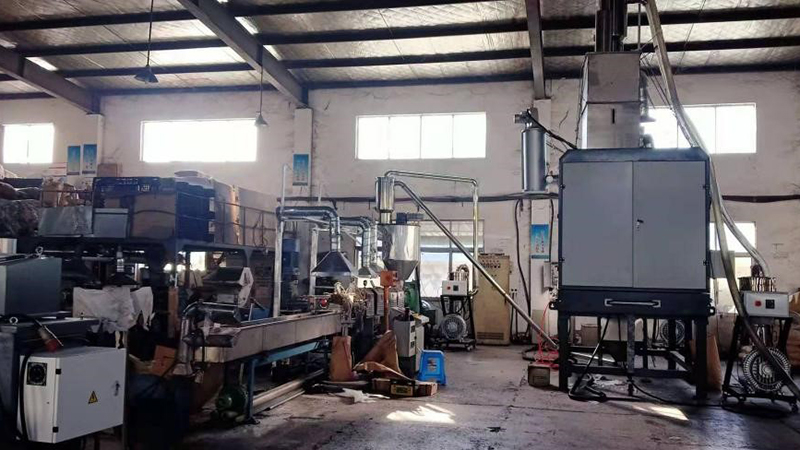
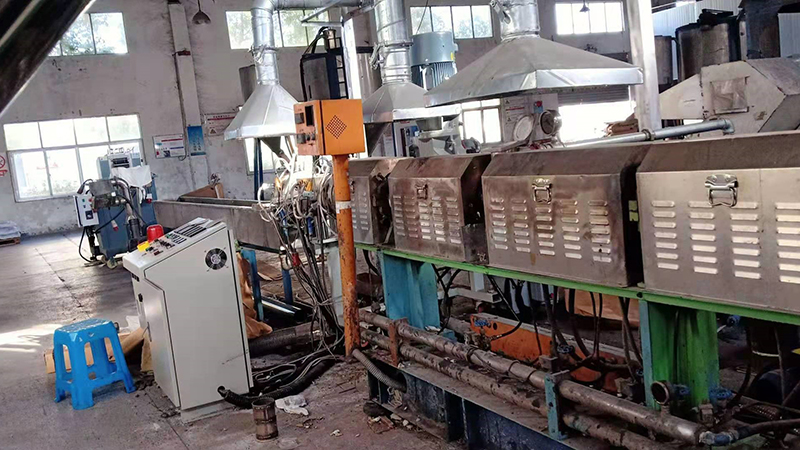
Infrared Pre-Drying of PET Flakes: Increasing Output and Improving Quality on PET Extruders
>>Reprocessing the flakes in the extruder reduces IV due to hydrolysis i the presence of water, and that’s why pre-drying to a homogeneous drying level with our IRD System can limit this reduction. In addtion, the resin does not yellow because drying time is reduced ( Drying time only needs 15-20mins, final moisture can be ≤ 50ppm, energy consumption less than 80W/KG/H), and shearing in the extruder is thereby also reduced because the preheated material enters the extruder at constant temperature”
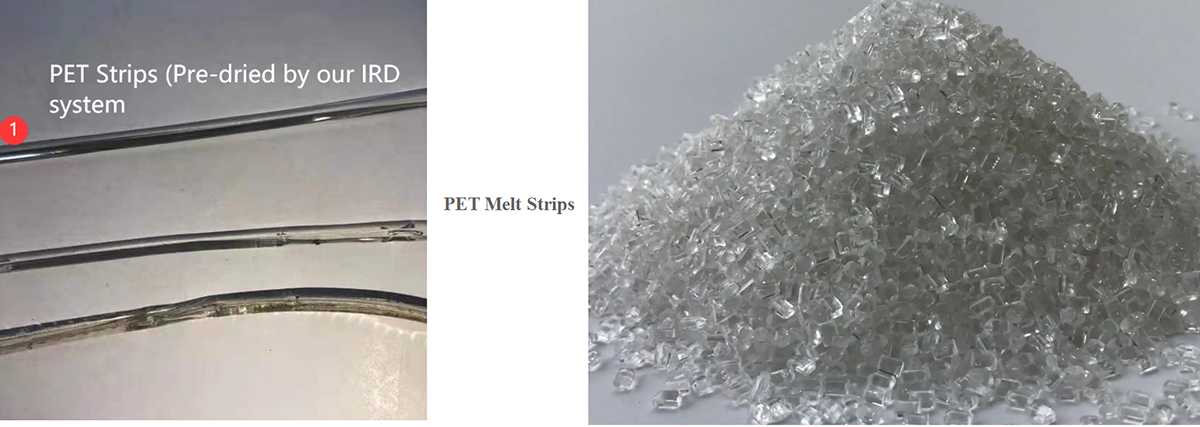
>>In a first step, the PET regrind is crystallized and dried inside the IRD within a period of roughly 15 minutes. This crystallization and drying process is achieved by a direct heat-up procedure using Infrared radiation, to achieve a material temperature of 170˚C. In contrast to the slow hot-air systems, the quick and direct energy input facilitates a perfect egalisation of permanently fluctuating input moisture values – the control system of the IR radiations allows responding to altered process conditions within seconds. In this way, values ranging between 5,000 and 8,000 ppm are reduced homogeneously inside the IRD to a residual moisture level of about 30-50ppm.
>>As a secondary effect of the crystallization process in the IRD, the bulk density of the ground material increases, especially in very light-weight flakes. This secondary effect is very interesting against the background that the tendency towards thin-walled bottles prevents the recycling material from achieving bulk densities of > 0.3 kg/dm³. An increase of the bulk density by 10 to 20 % can be achieved in the IRD, which appears to be insignificant at first sight, but improves the feed performance at the extruder inlet substantially – while the extruder speed remains unchanged, there is a substantially improved filling performance on the screw.
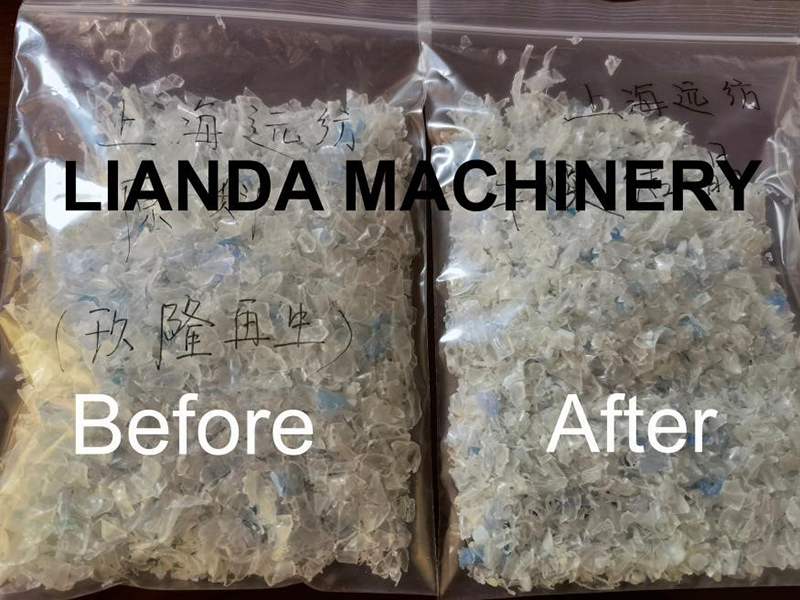
Post time: Apr-07-2023