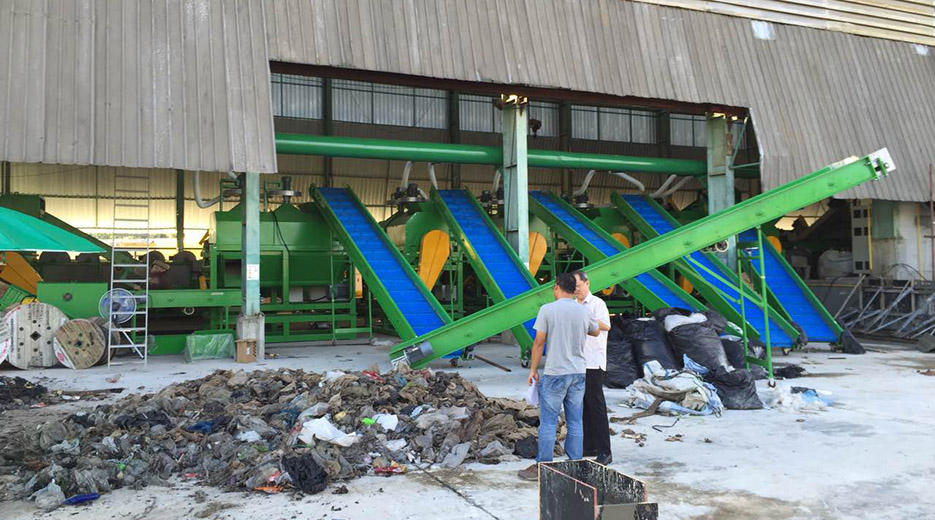
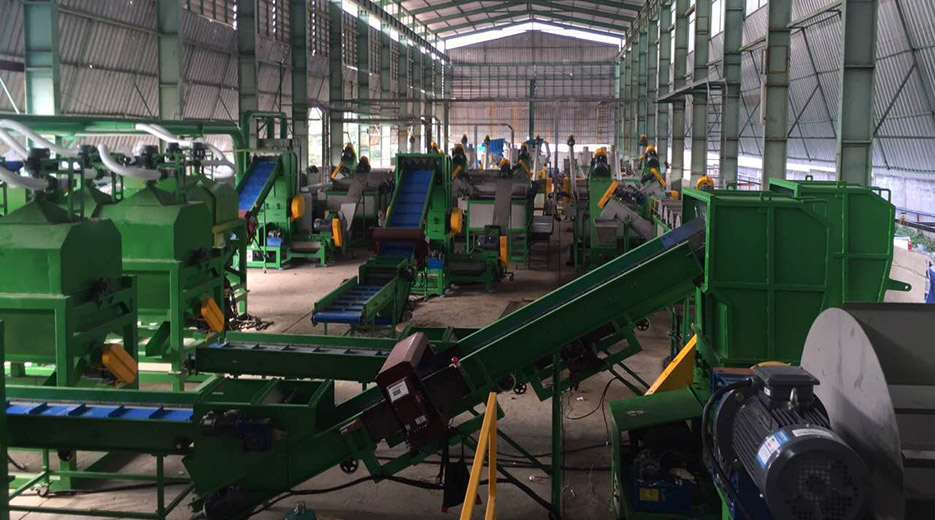
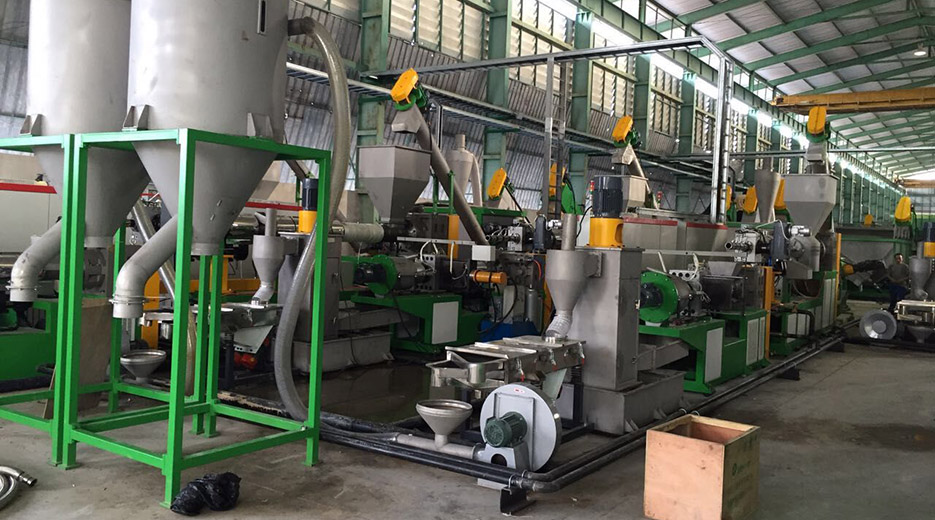
Export to Thailand:
The whole processing: Sorting--- Cutting---Washing--- Drying --- Granulating. The particle will be sold for making pipes. Vase etc.
>> To recycle Land-fill film cutting, washing, drying and granulating line
>> Bought 15 production lines from us
MSW film is mainly dominated by disposable film bags, with more sediment, grease and debris than normal agricultural films and industrial films. Before the MSW films reach the processing plant, they are sorted and pre-packaged manually. During the early investigation stage, the project manager gave us three requests: Firstly, shred the materials as a whole package, reducing the wearing of blades. Secondly, water conservation should be achieved while cleaning is thorough. Thirdly, subsequent drying process should be of low power consumption. Through several times of face-to-face discussion with engineers, we came up with the solution.
1. The film shredder is designed specifically LIANDA MACHINERY for waste films. The surface of blade rollers has high strength wear-resistant welding, to prevent the film winding and the wear of the blade rollers. The angle of the alloy steel blades can be swapped. The blades don't require sharpening with advantages of long service life, low energy consumption, large torque, high output and convenient to shred the whole package.
2. The friction washer and separation sedimentation tanks, made by stainless steel, can effectively remove the sediment and other impurities attached to the film surface. The waste water in the cleaning pool is recycled for energy saving.
3. The Film squeezing pelletizing dryer uses low-speed high torque screw and automatically controlled extrusion to make the water content reach 3-5%, thus solve the problems of high water content by conventional centrifugal method and high energy consumption by hot air drying.
4. Double step granulating machine line: Adopt special screw structure design for wet film. Double step of screen filteration system to remove the impurities. Adopt no-screen automatic clean system, save labor cost
Advantage:
• Crystallization& Drying only need 20mins
• Energy saving 45-50%
• No material clumping, no pellets sticking (Rotary drum design to avoid any clumping of the material ;Assure a very good cross mixing of the material)
• Uniform degree of crystallization
• Easy clean and easy change colour & material (The drum is designed with the simple mixing elements, there are no hidden spots and can be cleaned easily with a vacuum cleaner or compressed air.This enables the operator to have a very quick change from one material to another material and also the masterbatch colour)
• Siemens PLC automatically control (Recipes and process parameters can be stored in the controlling system to ensure optional and reproducible results)
Post time: Nov-26-2021