Infrared Rotary Dryer for PET Fiber making
Product Details
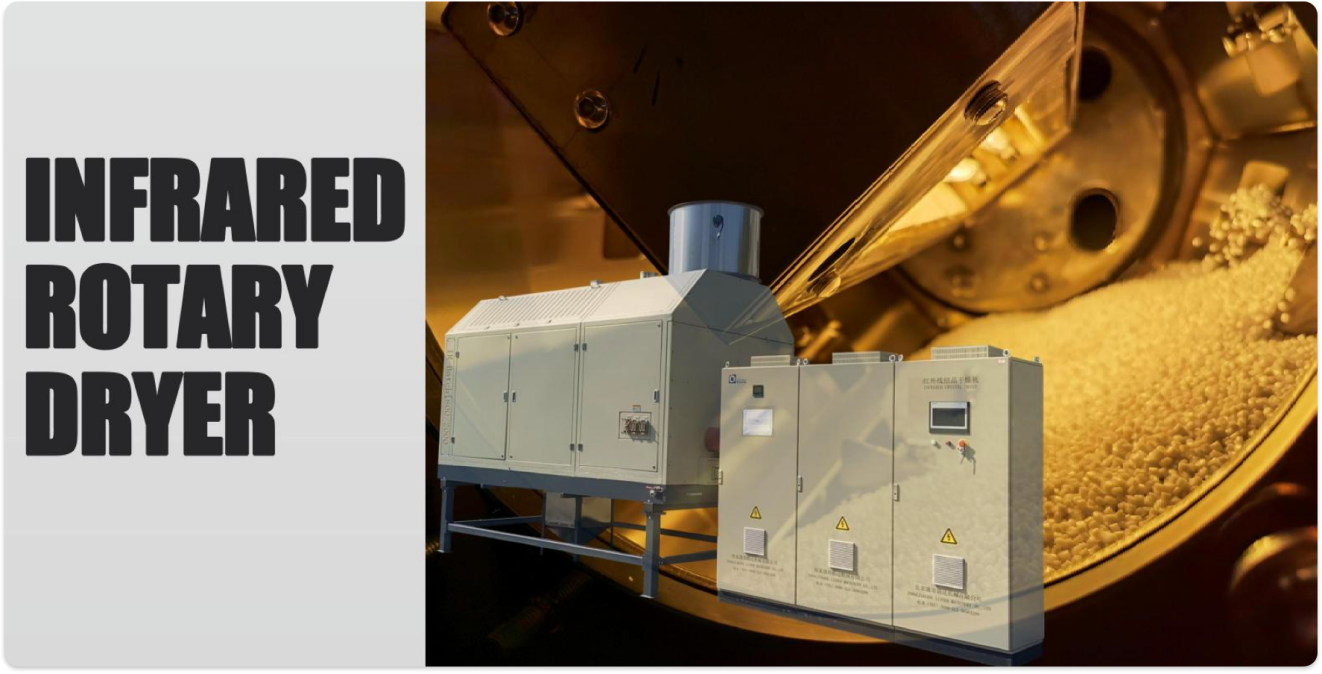
The infrared rays that penetrate and reflect from the material do not affect the organization of the material, but the absorbed tissue will be converted into heat energy due to molecular excitation, which causes the temperature of the material to rise quickly.
Heat to the core. By means of short-wave infrared light the material is heated directly from the inside
From the Inside to the outside. The energy in the core heats the material from the
inside out, so the moisture is driven from the inside to the outside of the material .
Evaporation of moisture. The additional air circulation inside the dryer removes the evaporated moisture from the material.
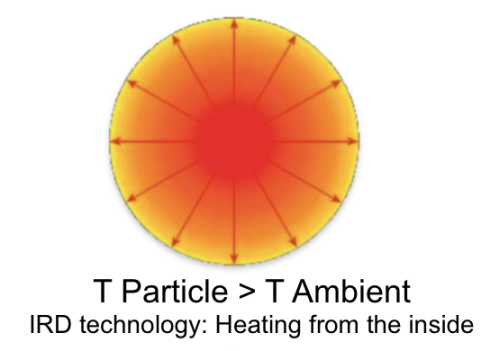
Case Study
Processing Shown
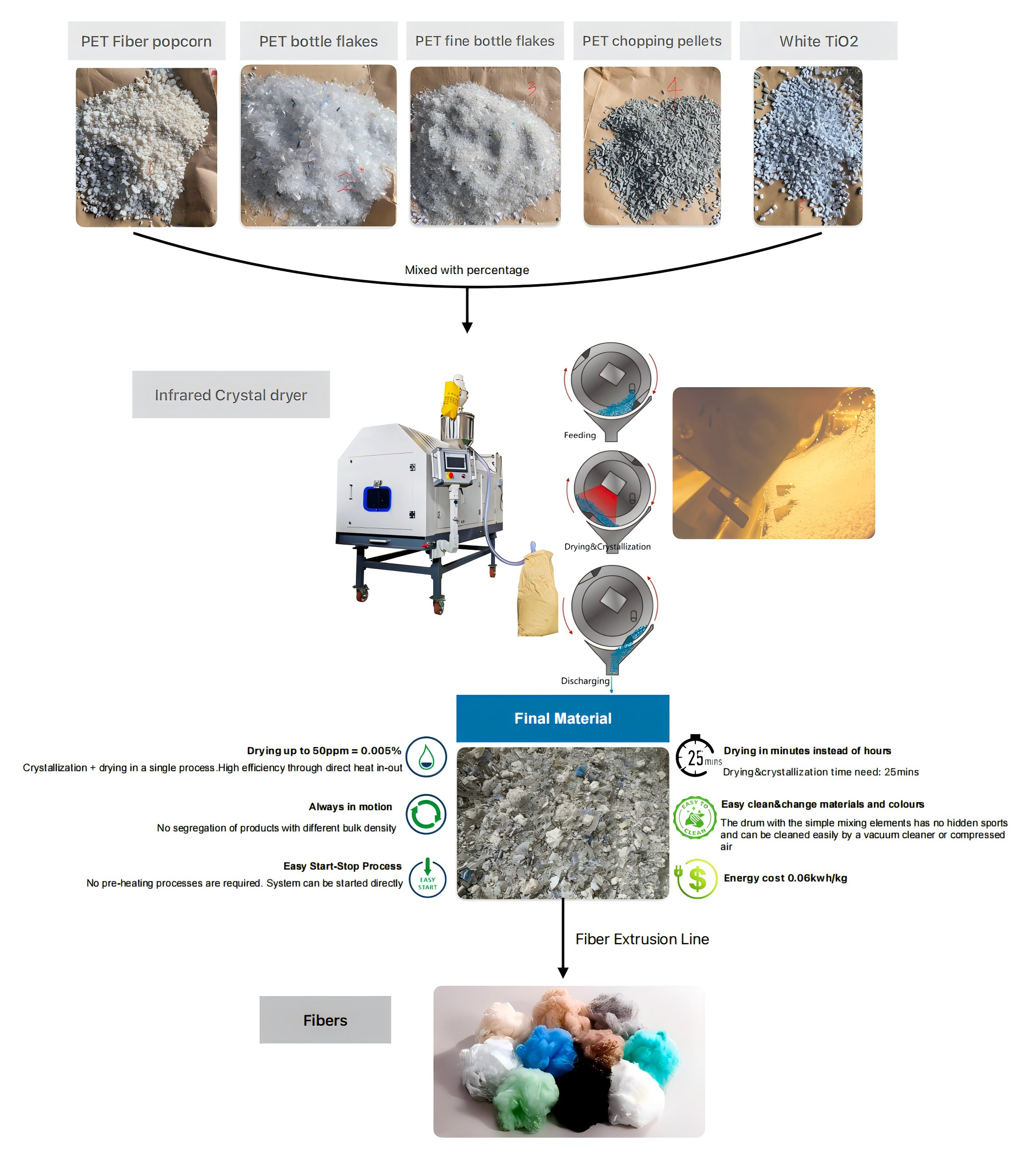
Advantage what we make in the processing
①Instant start and quick shut down
→An immediate start of the production run is possible.A warm-up phase of the machine is not required
→Processing can be started, stopped and restarted easily
② Always in motion
→No segrigation of products with different bulk density
→The perment rotation of the drum keeps the material moving and clumping can be avoided
③ Drying in minutes instead of hours ( Drying&crystallization time need: 25mins )
→Infrared rays caused molecular thermal pscillations which directly act on the core of the particles from the inside out. so that the moisture inside the particles is rapidly heated and evaporated into the circulating ambient air,and the moisture is removed at the same time
④ Imrpoving the ouput of PET Extruder
→ An increase of the bulk density by 10-20% can be achieved in the IRD system, improve the feed perfirmance at the extruder inlet substantially, while the extruder speed remains unchanged, there is a substantially improved filling performance on the screw
⑤ Easy clean&change materials and colours
→ The drum with the simple mixing elements has no hidden sports and can be cleaned easily by a vacuum cleaner or compressed air
⑥ Energy cost 0.06kwh/kg
→ short residence times = high process flexiblility
→ energy individually adjustable --- Each lamp can be controlled by PLC programme
FAQ
a.What’s the limit on the intial moisture of the raw material?
→ No exact limition on initial moisture, 2%,4% are both ok
b. What’s the final moisture can get after dried?
→ ≦30ppm
c.What’s the drying&crystallization time need?
→ 25-30mins. The drying & crystallized will be finished in one step
d.What’s the heating source? Low dew point dry air?
→ We adopt infrared lamps (infrared wave) as heating source.By means of short-wave infrared light the material is heated directly from the inside to the outside. The energy in the core heats the material from the inside out, so the moisture is driven from the inside to the outside of the material .
e. Will the different density material be layered suring the drying processing?
→ The perment rotation of the drum keeps the material moving,--No segrigation of materials with different bulk density while fed to the extruder
f. What’s the drying temperature?
→ The drying temperature set scope: 25-300℃. As PET, we suggest to adopt about 160-180℃
g. Is it easy to change colour masterbatch?
→The drum with the simple mixing elements has no hidden sports, easily to change material or color materbatch
h.How do you deal with the powder?
→ We have dust remover which will work with IRD together
I. What's the woking life of the lamps?
→ 5000-7000hours. (It doesn’t mean the lampscan’t work any more, only power attenuation
J.What’s the delivery time?
→ 40 working days after getting deposit
if you have more details you’d like to know, please send us the E-mail:
Running in customer factory reference
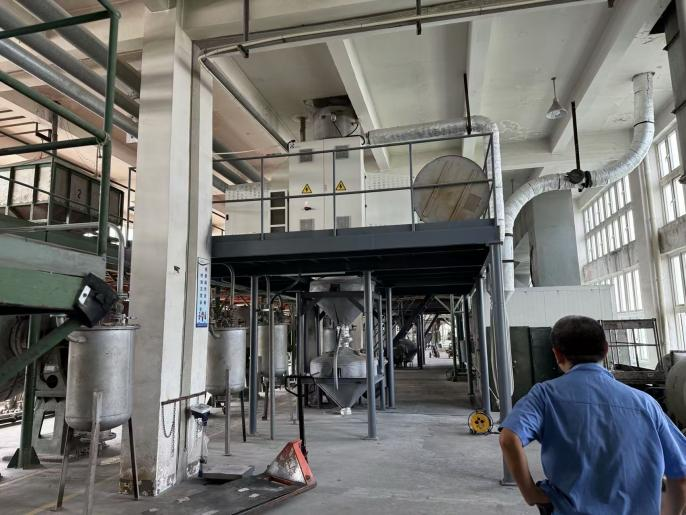
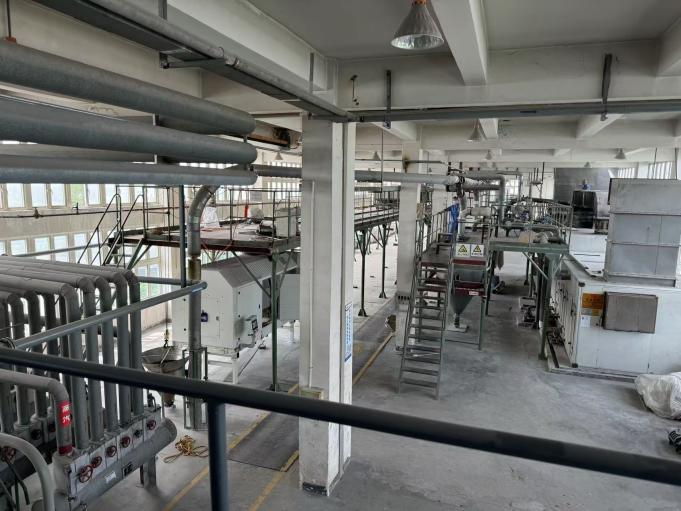
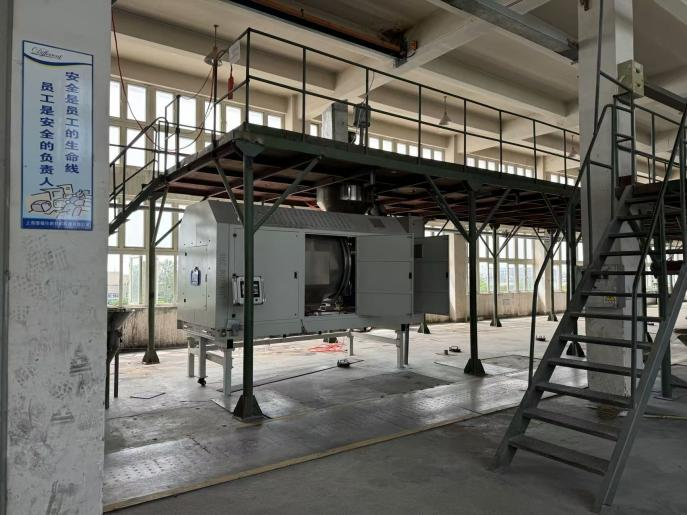
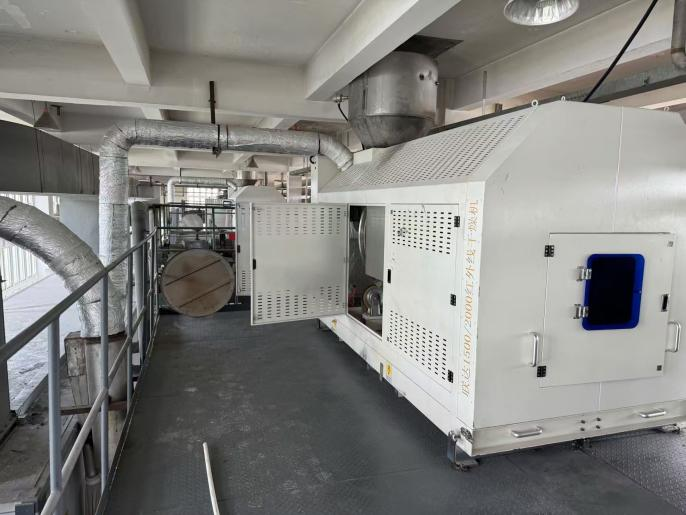
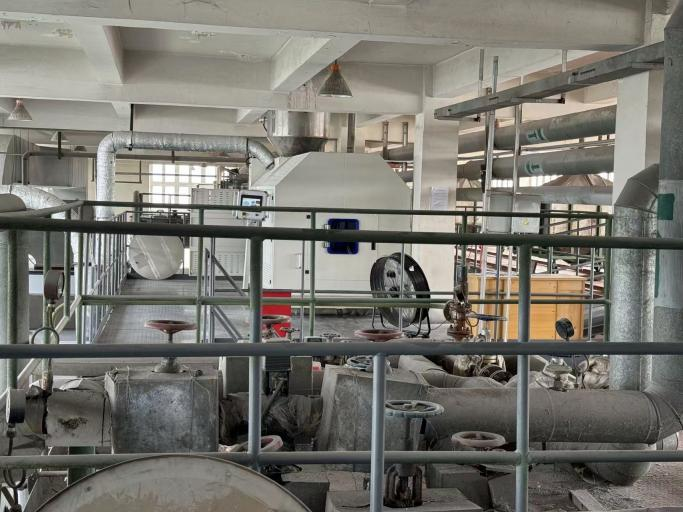
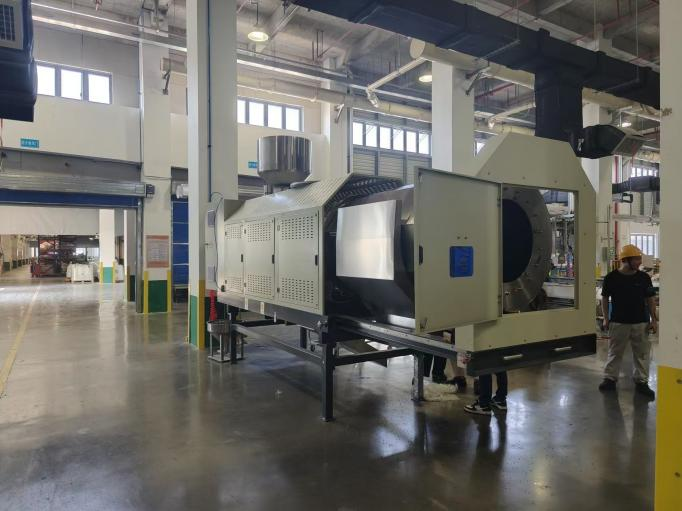
Our Service
Our factory has build Test Center. In our Test center, we can perform continuous or discontinuous experiments for customer’s sample material. Our equipment is furnished with comprehensive automation and measurement technology.
- We can demonstrate --- Conveying/Loading, Drying& Crystallization, Discharging.
- Drying and crystallization of material to determine residual moisture, residence time, energy input and material properties.
- We can also demonstrate performance by subcontracting for smaller batches.
- In accordance with your material and production requirements, we can map out a plan with you.
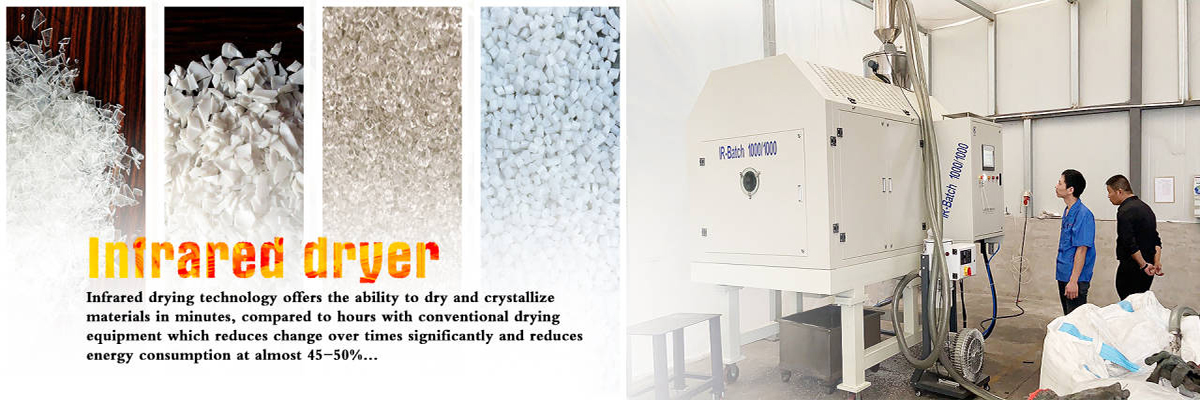
Experienced engineer will make the test. Your employees are cordially invited to participate in our joint trails. Thus you have both the possibility to contribute actively and the opportunity to actually see our products in operation.