Infrared drying can significantly improve the performance of a twin-screw extruder because it reduces the degradation of IV value and significantly improves the stability of the entire process.
First , the PET regrind will be crystallized and dried in about 15-20 minutes inside the IRD. This crystallization and drying process is achieved by a direct heating procedure using infrared radiation to achieve a material temperature of 170 °C. Compared to slow hot-air systems , quick and direct energy input contributes to the perfect balance of permanently fluctuating input moisture values - infrared radiation control systems can respond to changing process conditions in seconds. In this way, the value in the range of 5,000 to 8,000 ppm inside the IRD is uniformly reduced to a residual moisture content of about 150-200 ppm.
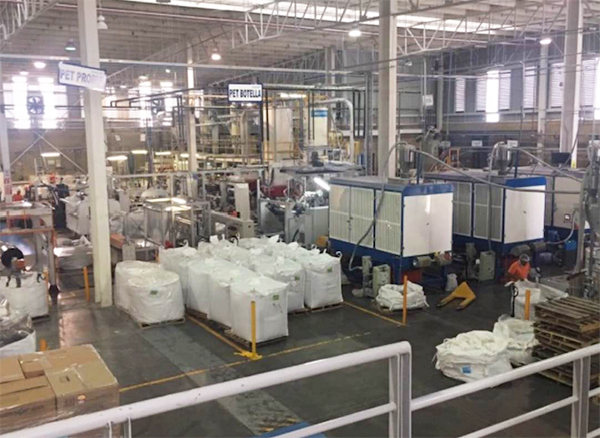
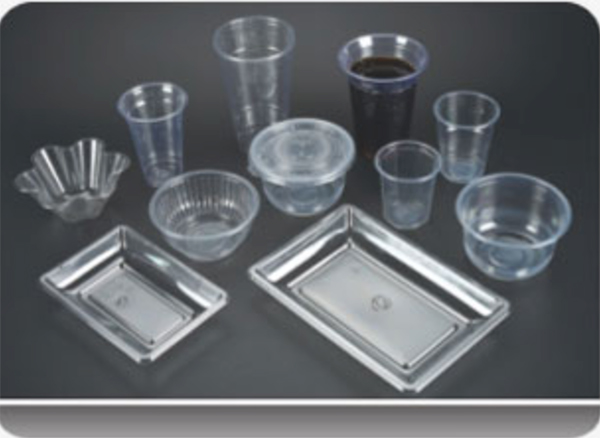
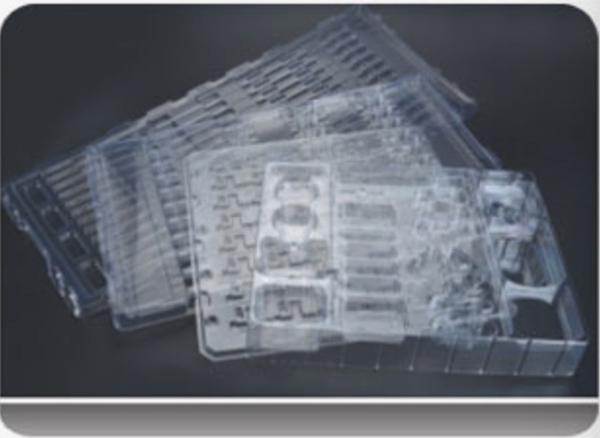
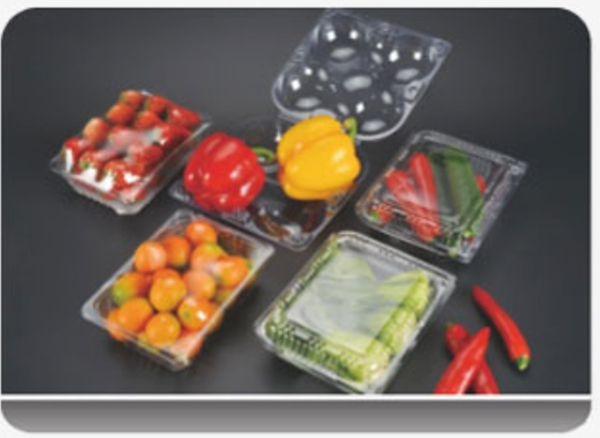
As a secondary effect of the crystallization process in the IRD, the bulk density of the crushed material increases, especially in very light weight flakes. In this condition: IRD can increase the bulk density by 10% to 20%, which may seem very small difference, but can significantly improve the feed performance at the extruder inlet - although the extruder speed remains the same, it can greatly improve the screw filling performance.
As an alternative to high temperature crystallization and drying systems, the IRD system can also be designed as a fast dryer to operate efficiently and at a drying temperature below 120 °C. In this case, the moisture content achieved will be limited to "only" about 2,300 ppm, but in this way it can be reliably maintained, especially within the range of values specified by the extruder manufacturer. Another important factor is the avoidance of high and permanent fluctuations in the value, with a moisture content reduction of up to 0.6% which will greatly reduce the IV parameter in the molten plastic material. The residence time in the dryer can be reduced to 8.5 minutes and the energy consumption is less than 80 W / kg / h
Post time: Feb-24-2022