PET Bottle Flake Granulation Line
PET Bottle Recycling Pelletizer PET Granulation Machine Process flow
Technical Specification
Machine Name |
PET Single Screw Extrusion pelletizing Line |
Raw Material |
rPET Flakes |
Final Product |
rPET Pellets |
Production Line components |
Infrared crystal dryer system: Vacuum feeder/ Infrared crystal dryer/ Vacuum discharger
Single Screw Extrusion granulating line: Single screw main extruder/Hydraulic Double Pistons screen changer/Die head/Flushing water trough/Flushing pellitizer/Vertical dewatering machine/Vibrating sieve machine/ Storage
|
Screw diameter |
90mm-150mm |
L/D |
1:24/1:30 |
Output range |
150-1000KG/H |
Screw material |
38CrMoAlA with Nitrding Treatment |
Pelletizing Type |
Water flushing & pelletizing |
Screen changer |
Hydraulic Double Pistons Screen Changer |
Machine Details
Infrared Crystal Dryer (LIANDA PATENT DESIGN)
①Improving the manufacturing and physical properties of recycled, food-grade PET through technology powered by infrared wave has a crucial part to play in the intrinsic viscosity (IV) property
②Pre-crystallization &drying of the flakes prior to extrusion helps minimize the loss of IV from PET, a critical factor for reuse of the resin
③Reprocessing the flakes in the extruder reduces IV due to hydrolysis in the presence of water, and that’s why pre-drying to a homogeneous drying level with our IRD System can limit this reduction.
In addition, the PET melt strips does not turn yellow because drying time is reduced ( Drying time only needs 15-20mins, final moisture can be ≤ 30ppm, energy consumption less than 60-80W/KG/H)
④Shearing in the extruder is thereby also reduced because the preheated material enters the extruder at constant temperature”
⑤Improving the output of PET Extruder
An increase of the bulk density by 10 to 20 % can be achieved in the IRD, improves the feed performance at the extruder inlet substantially – while the extruder speed remains unchanged, there is a substantially improved filling performance on the screw.
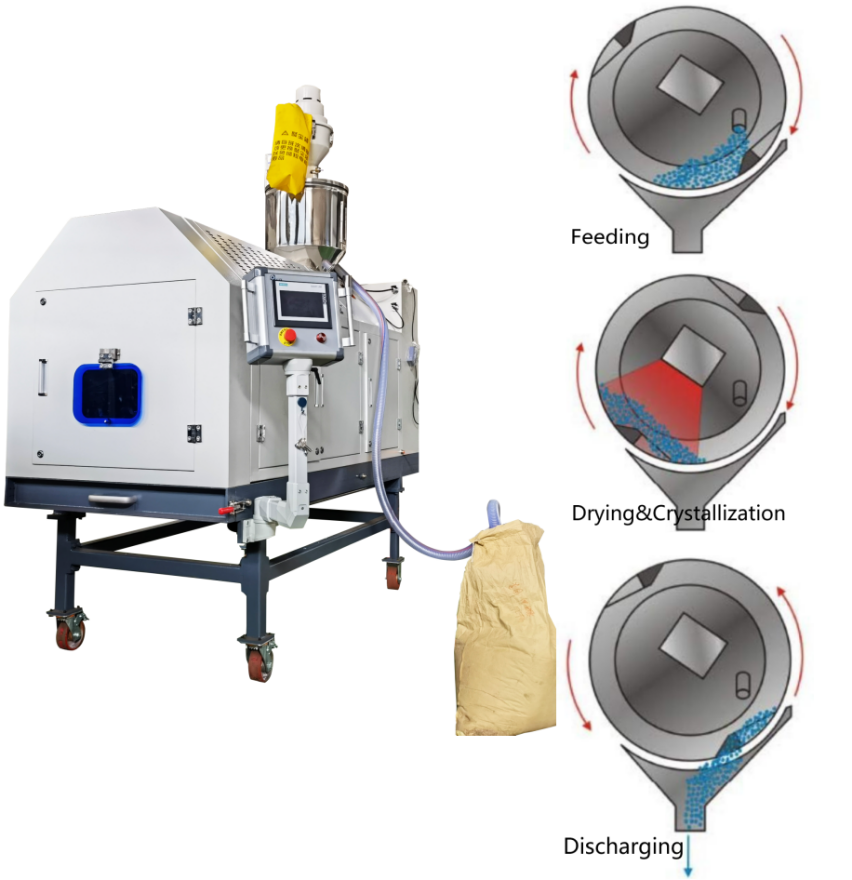
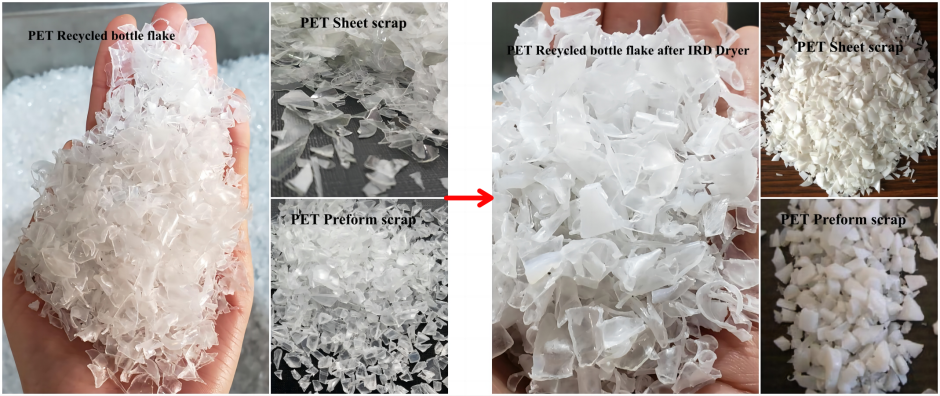
Single Screw Extrusion Pelletizing Line (Without Vacuum Venting)
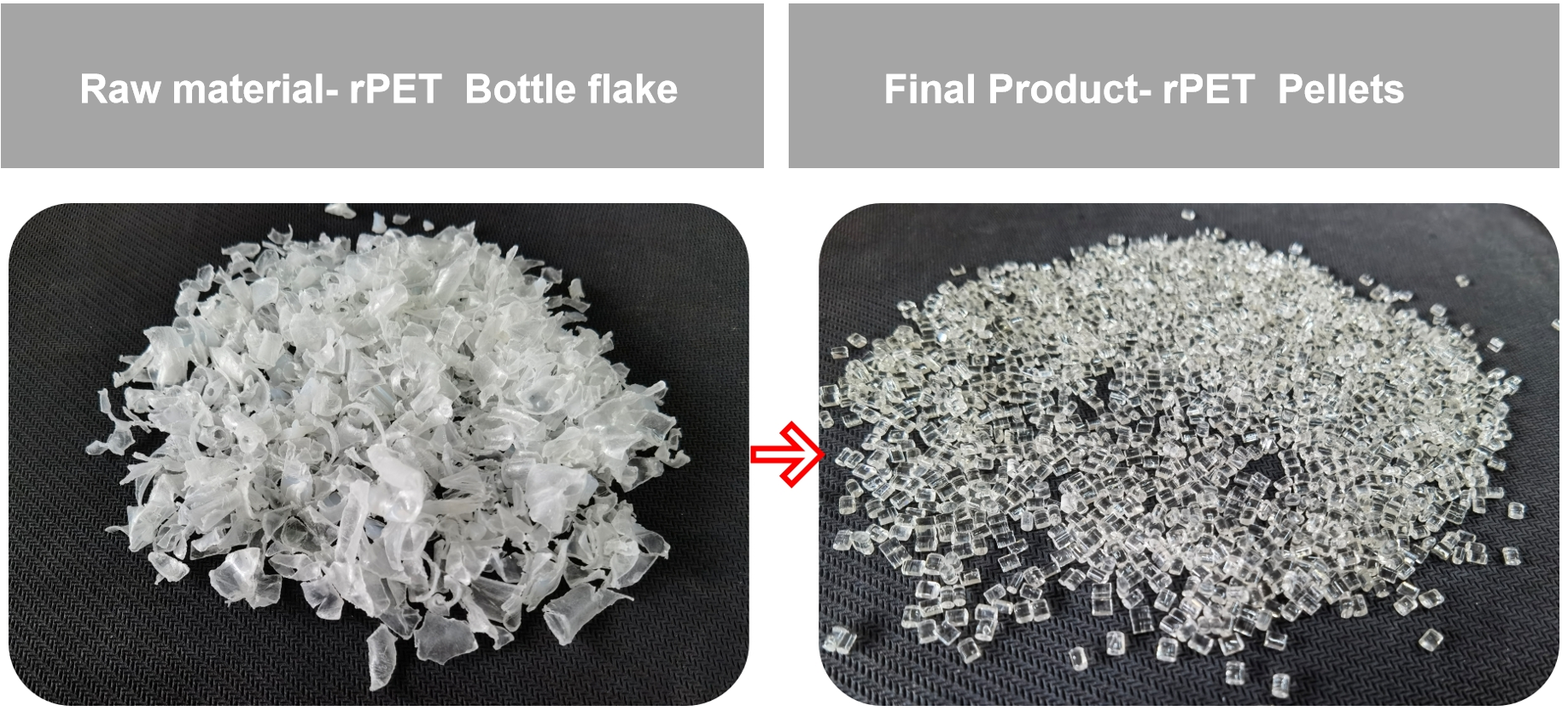
Utilizing the strengths of Single screw extruder and paring it with LIANDA uniquely designed screw for rPET Bottle flakes, we were able to increase the capacity by 20% with less power consumed compared with Parallel double screw extruder.
Viscosity of rPET pellets produced by our system: there is only ≤0.02-0.03dl/g viscosity drop ---without adding any viscosity enhancer. ( According to our in-house testing)
rPET pellets Colour: transparent --- without adding any transparency enhancer
Without Vacuum venting system --- Saving energy cost, trouble-free and stable working
Machine Photos
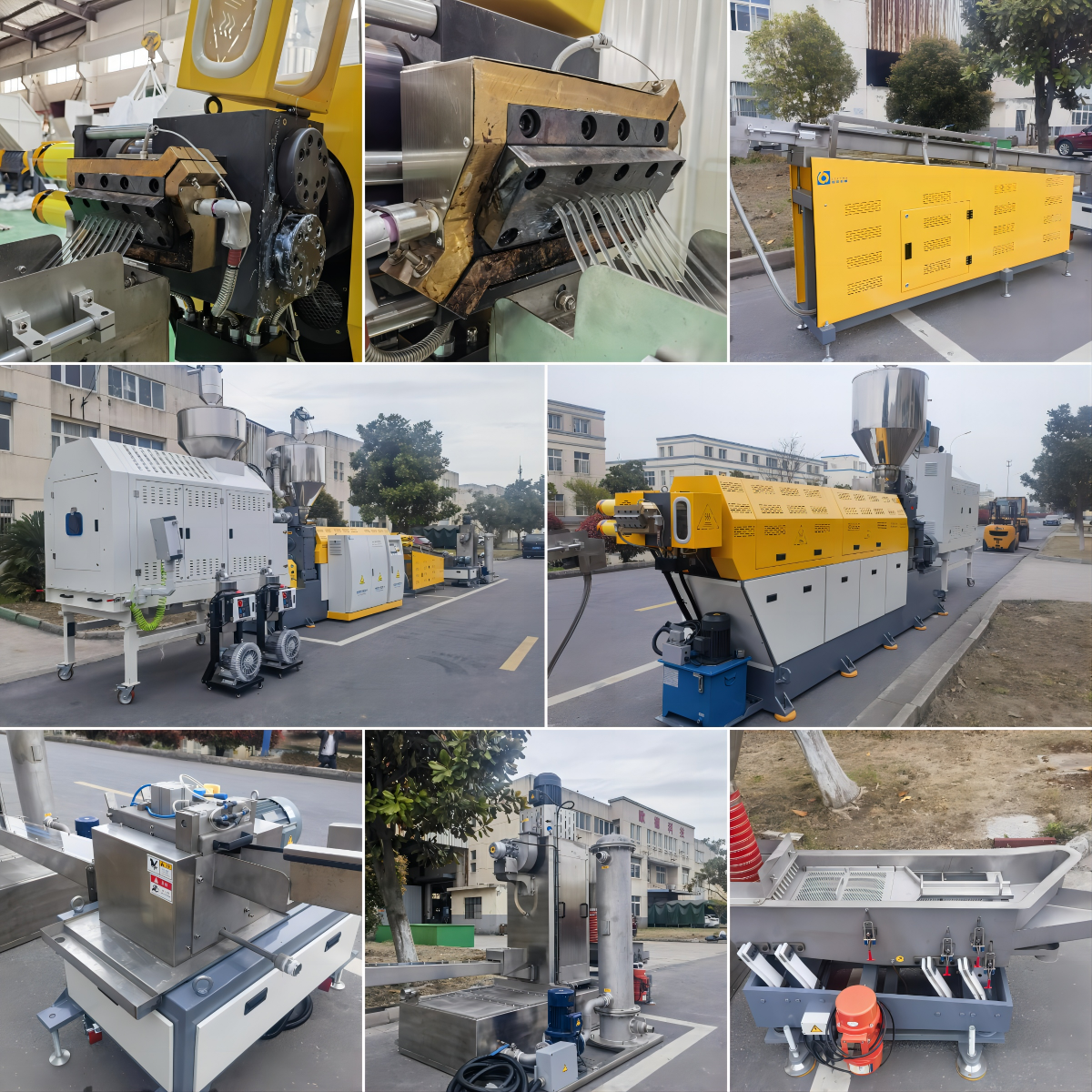
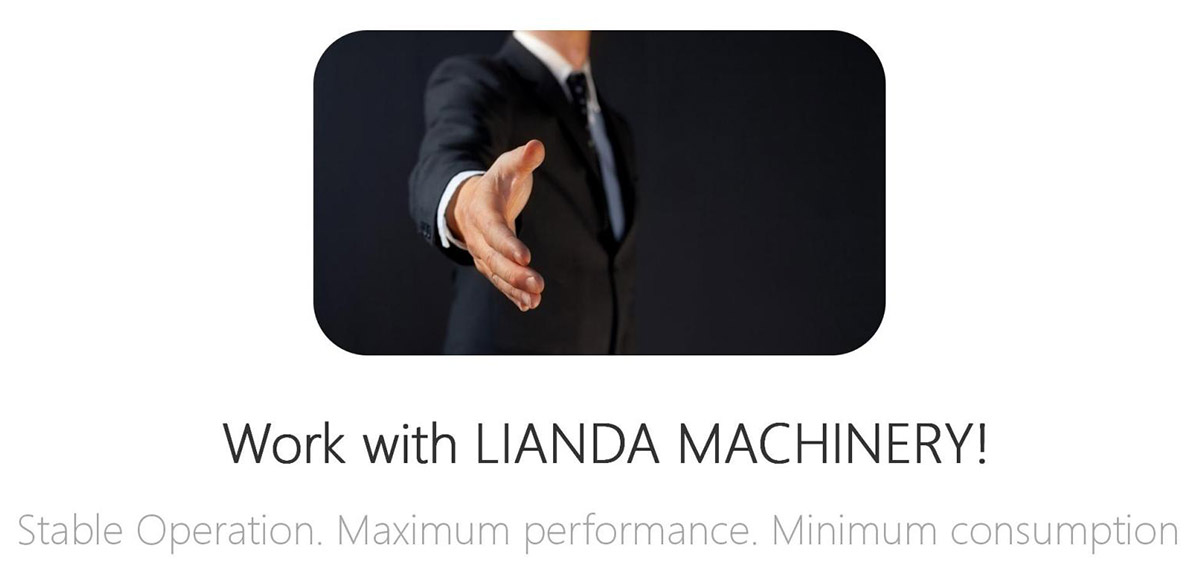