Mulch film washing recycling line
Mulching Film Recycling Machine Line
Lianda Machinery has been specialized as the manufacture of waste plastic film, agricultural waste film processing equipment for more than 20years. The equipment is constantly updated, improved and upgraded and has gradually formed a complete and mature recycling program.
>>After the waste film is collected, it will be pre-processed --- Pre-cut or shred the large rolls/bales of waste film into smaller size, and then fed the sand remover machine to have sand removal treatment, because too much sediment content will reduce the crusher blades working life, which will also affect the cleaning quality.
>>The film will be low sand content after sand-remover machine, Then it enters the crusher for fine crushing treatment. When crushing, water is added for crushing, which can play a role of preliminary cleaning.
>>The bottom of the crusher is equipped with an eccentric friction elution machine, which can wash out the mud and dirty water on the film. The section is filled with water for friction cleaning, and the cleaned sediment is above 99%.
>>The cleaned film enters the sink and floats rinsing tank for rinsing, and the rinsed film material is dug into the squeezing machine by the excavator for squeezing and dewatering. Subsequent to be connected to the granulating line to make granules.
Processing Flow
①Raw Material: Mulching film/Ground film →② Pre-cutter to be short pieces →③ Sand remover to remove the sands →④ Crusher cutting with water →⑤ High speed friction washer washing&dewatering →⑥ Forced strong high speed friction washer →⑦ Double step floating washer →⑧ Film squeezing&pelletizing dryer to dry the washed film at the moisture 1-3% →⑨ Double step granulating machine line to make pellets →⑩ Package and selling the pellets
Production Line Requirement For Reference
No |
Item |
Need |
Note |
1 | Production line Space Need L*W*H (mm) | 420000*3000*4200 | |
2 | Workshop need | ≧1500m2
Including raw material storage area and Final product storage area |
|
3 | Total installation power | ≧180kw
Refer to the production line as mentioned above |
Energy consumption ≈70% |
4 | Water consumption | ≧15m3 per hour ( With circulate water ) | |
5 | Labour need | Feeding ---- 2person
Package ---- 1person The production line operator ----1person Fork lift ---- 1unit |
Pre-Cut By Hydraulic Shearing
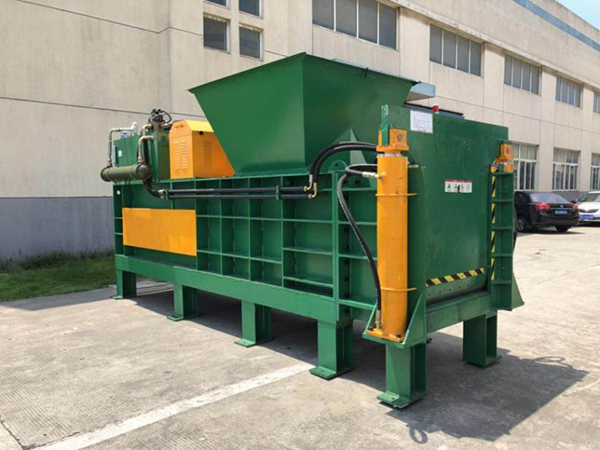
>> Pre-cut the long mulching films to short pieces for Sand remover feeding
Sand&Grass Remover
>>Sand remover is mainly used for removing the sand, grass, leaves mixed with Agricultural film. Sand remover adopt air pressure to separate the heavy material from the light material.
>>Advantages:
■The sand remover will work without water
■High efficiency with lower power consumption
■Easily to operate, longer working life
■To pre-wash the agricultural film, to protect the crusher blades and save water consumption
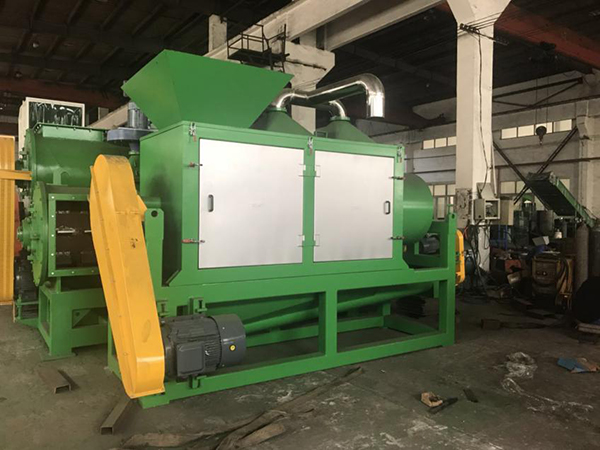
Film Crusher
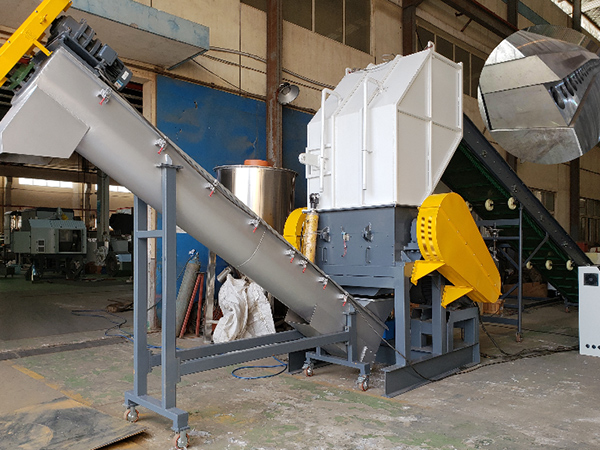
In the Rough and fine crushing process, according to the characteristics of strong toughness and high entanglement of LDPE film and PP woven bags, we have designed a double V-shaped crushing knife holder and a back knife-type knife installation structure which will enlarge the capacity to be double, but less electrical energy cost
>> Adopt Double V blade frame, back knife structure, Double output
■ Compared with the other Film recycling washing line, it reduces the electrical cost, reduces the power supply load of the customer factory
Forced High Speed Friction Washer
>>For strong high speed friction washer and remove the dirty water before the film scrap enter into Floating washer
■ Rotating speed can be 1250rpm
■ Adopt specialized screw shaft design for Film, keep sure no stuck,working stable
■ With the function of de-watering
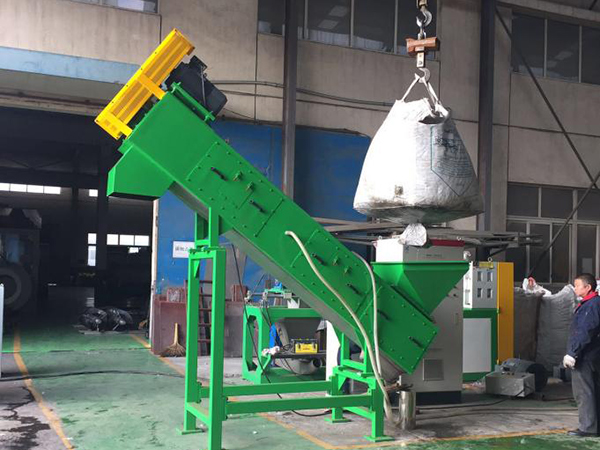
Floating Washer
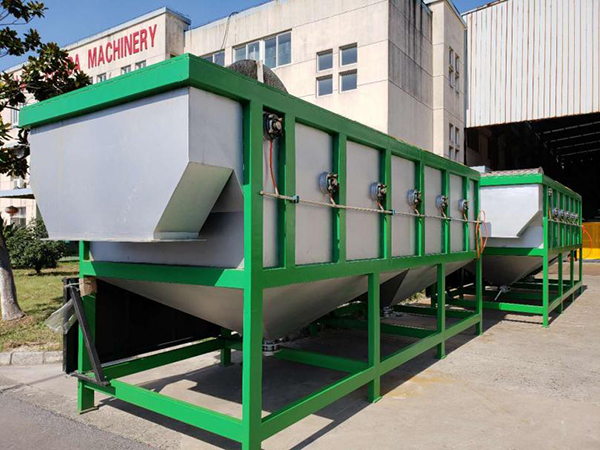
>>Adopt the “ V” type bottom design.
■The bottom of the rinsing tank is equipped with a plurality of conical slag discharge devices. When there is too much dirt or sediment at the bottom of the pond, just open the slag discharge valve to discharge the sediment at the bottom of the tank, without changing the whole pool water. Save water consumption
>>In the rinsing and discharging process, the chain plate reverse tangent digging discharging method is adopted instead of traditional discharging methods
Film Squeezing Pelletizing Dryer
>> Remove the water of the washed film by screw pushing and electrical magnetic heating. with the screw squeezing and self-friction heating, the washed films will be had high degree of drying & half plasticized, low power consumption, high output. The final moisture is about 2%.
>>The screw barrel is made of material feeding barrel, compressing barrel and plasticized barrel. After feeding, squeezing, the film will be plasticized and cut to particle by the pelletizer which is installed besides the mold
■Uniform feeding without stuck
■Make water removing more than 98%
■Less energy cost
■Easily for feeding the particle to the extruder and enlarge the capacity of the extruder
■Stable the quality of finished particle
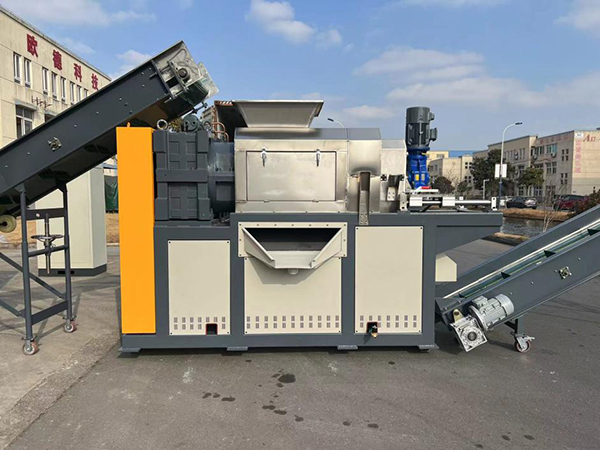
Application Samples Shown
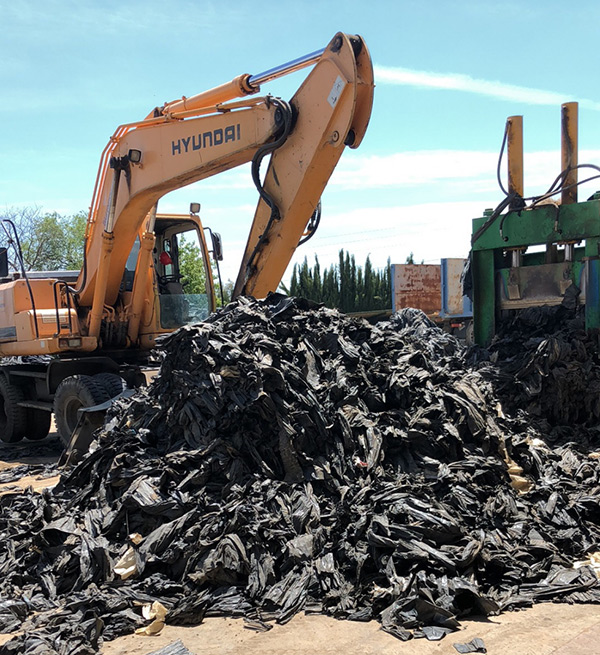
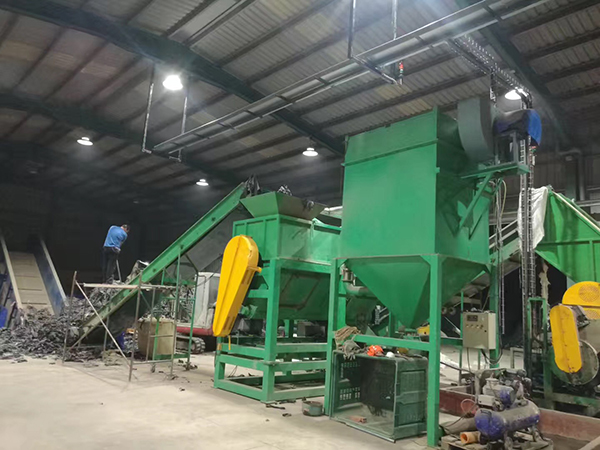

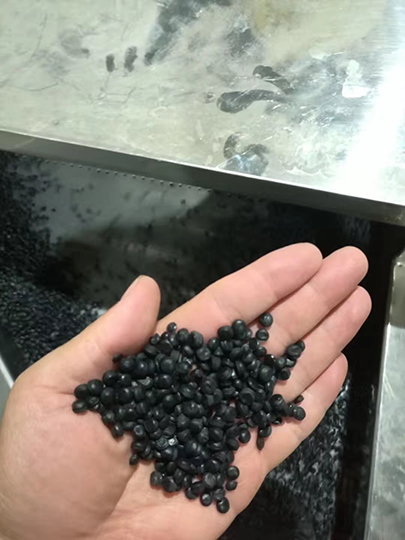
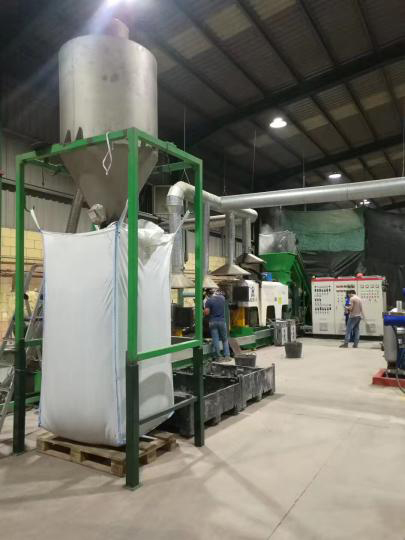

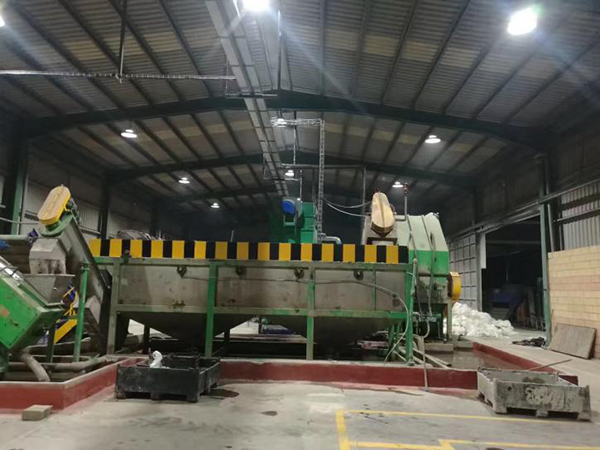
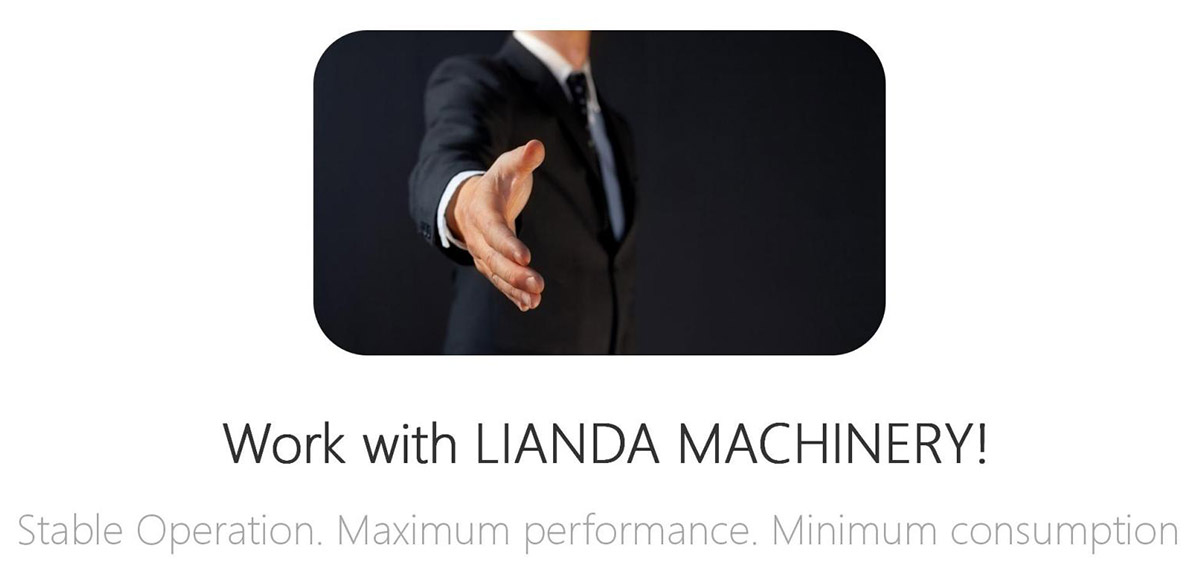